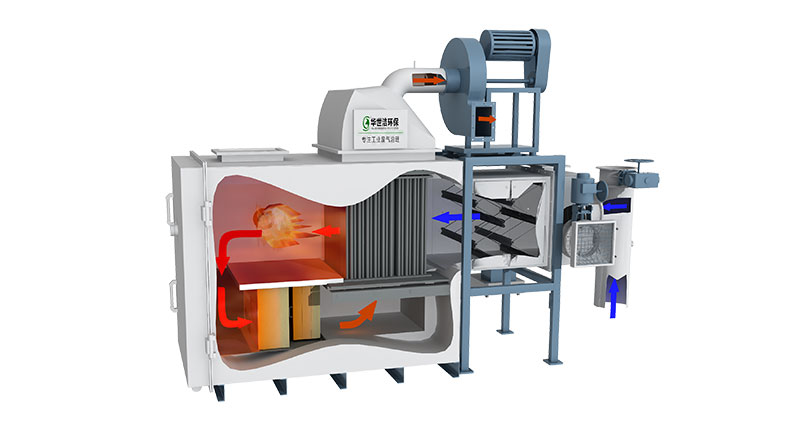
Product overview
Co uses catalytic combustion technology to make the organic waste gas burn without flame under the condition of lower starting temperature (300-400 ℃). In the process of catalytic combustion, the catalyst can reduce the activation energy, and the surface of the catalyst has adsorption function, which makes the reactant molecules concentrate on the surface to improve the reaction rate and accelerate the oxidation process. Compared with direct combustion, the catalytic combustion of organic waste gas has the characteristics of low starting temperature and low energy consumption. In some cases, no external heating is required after the ignition temperature is reached. The purification rate of organic waste gas treated by catalytic combustion is generally over 95%, and the final product is harmless CO2 and H2O (heteroatom organic compounds and other combustion products), so there is no secondary pollution. Co uses high performance catalyst, Pt and PD noble metal catalyst with ceramic support. The dispersion of noble metal active position is high, catalytic activity is high, service life is long, pressure loss is small, which reduces the total energy consumption of the whole machine.
Process principle description
CO
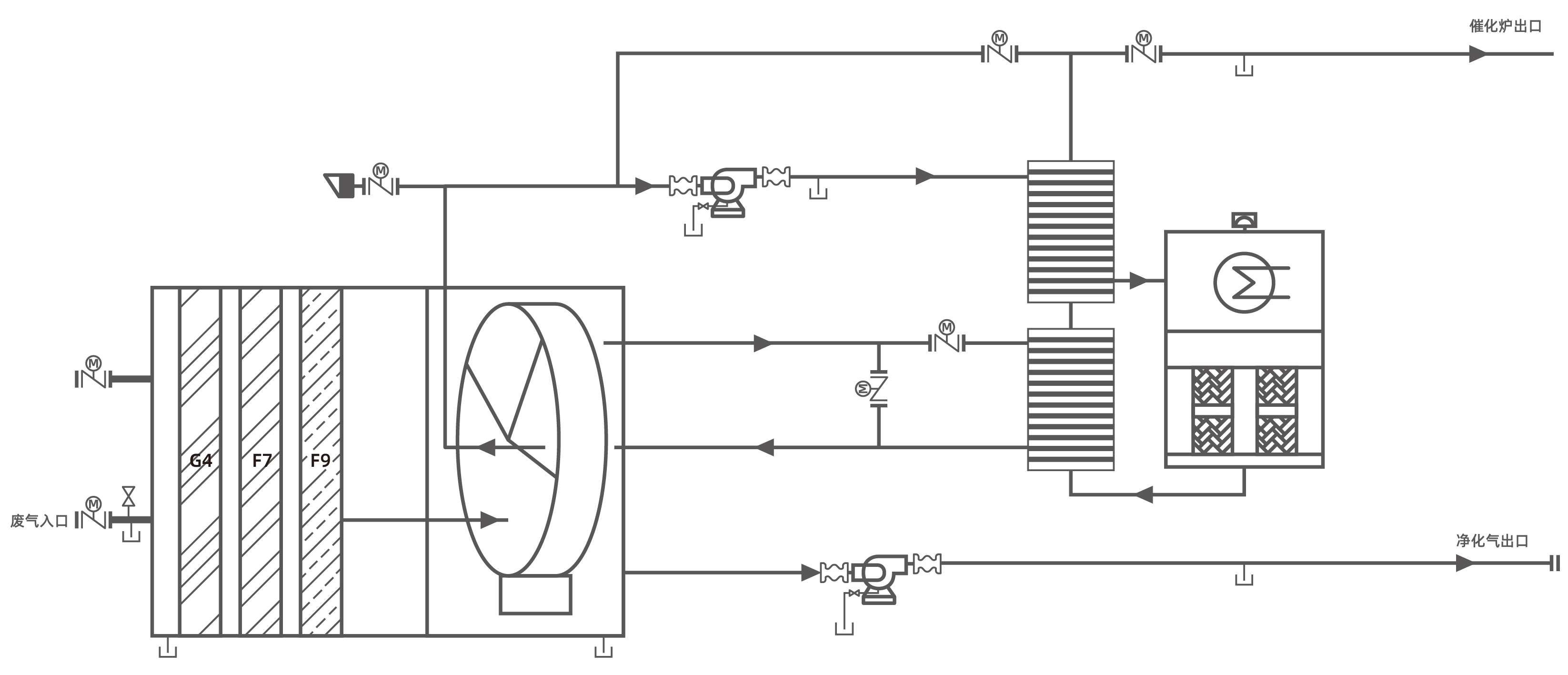
VOCs flow direction 1: driven by the desorption fan, low concentration VOCs gas from the cooling area of the molecular sieve rotor enters the cold side channel of the first stage heat exchanger for heat exchange, and the gas temperature rises from 60 ℃ to 200 ℃ and then flows back to the desorption sector of the molecular sieve rotor. High temperature gas desorbs a large number of VOCs molecules from the zeolite surface of the molecular sieve rotor to form high concentration VOCs, and the concentration is controlled below 10g / m3.
VOCs flow to two directions Driven by the desorption fan, the high concentration VOCs gas enters the cold side channel of the two-stage heat exchanger for heat exchange. The gas temperature rises from 120 ℃ to 300 ℃ and then enters the catalytic combustion chamber. The temperature meter in the catalytic combustion chamber checks the temperature of the VOCs gas after entering. If the temperature of the VOCs gas is lower than 300 ℃, the burner in the catalytic combustion chamber will ignite automatically to heat the gas again until the temperature is between 300 ℃ and 350 ℃. Then VOCs gas flows through the burner and then flows through the surface of catalyst to produce flameless combustion. The organic molecules in VOCs are oxidized and decomposed into CO2 and H2O, and a lot of heat energy is released at the same time. The specific heat ratio of VOCs is about 25 ℃ / g. when the concentration of VOCs is 10g / M 3, the temperature rises 250 ℃. Therefore, the temperature of 300 ℃ VOCs increases to 550 ℃ after catalytic combustion. After catalytic combustion, VOCs gas is oxidized and decomposed into clean high temperature gas, which flows through the hot side channel of the first stage heat exchanger and the hot side channel of the second stage heat exchanger to provide them with heat energy for heat exchange in the cold side channel, and then discharged into the atmosphere through the chimney. In the later design of waste heat recovery and utilization, the high-temperature and clean gas will also be recycled to provide heat energy for Party A's production workshop, hot water supply or environmental heating supply.
Product features and advantages
Advanced design concept: system integration, standardized / modular design makes the construction period more flexible / turnkey project, so that customers can leave the project to experts. |
Scientific and rigorous design means: using FLUENT software for numerical simulation/ The distribution of flow field and temperature field in CO equipment was optimized. |
Excellent and efficient operation performance: treatment efficiency up to 95% |
Reliable safety performance: explosion proof design, insulation monitoring and early warning / multiple safety interlock, to ensure efficient and safe operation. |
Convenient and fast network interaction performance: remote control, real-time online monitoring. |
Simple and efficient operation performance: modular management, programmed control, automatic operation / simple and efficient, convenient and fast maintenance. |
Application industry
Suitable for painting, spraying, printing and other industries
Air volume: 5000 ~ 1000000nm 3 / h
Components: ethyl acetate, propyl acetate, ethanol
Concentration: 200mg / Nm3 < concentration < 1200mg / Nm3
The inlet temperature of RCO is not lower than 300 ℃, and the outlet temperature is not higher than 600 ℃
- • VOCs adsorption and concentration treatment
- • Thermal oxidation/catalytic oxidation
- • Adsorption and recovery of high concentration VOCs
- • Biological treatment of odor VOCs
- • Industrial dust and oil mist filtration
- • Heat recovery
- • Dehumidification
- • Indoor purification
- • VOCs Online Monitoring Platform