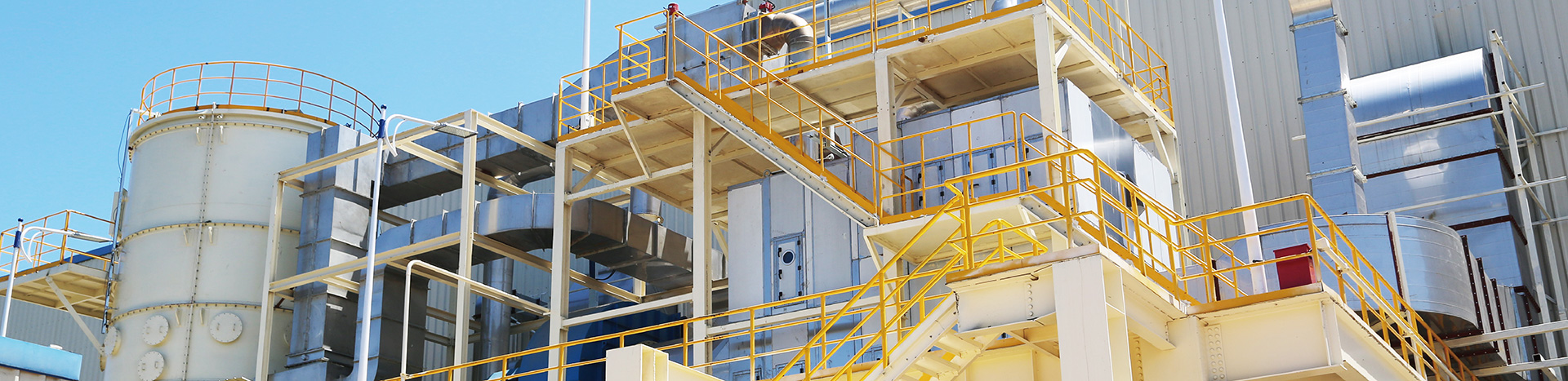
Product overview
Adsorption recovery is mainly to use adsorption materials to adsorb the organic solvent in the waste gas, and then desorption to recycle the organic solvent. In organic waste gas treatment process, adsorption is one of the methods with good treatment effect and wide application. Adsorbents include activated carbon, diatomite, zeolite and so on, among which activated carbon is the most widely used. Through the adsorption system, not only the VOCs concentration in the exhaust gas can be greatly reduced, and the exhaust gas can be discharged up to the standard, but also the collected materials can be reused for production through desorption, so as to realize the material recycling and reduce the material consumption.
Process principle description
Adsorption: the waste gas containing VOCs passes through the adsorbent bed, VOCs are adsorbed in the microporous structure of the adsorbent, and the clean gas is discharged into the atmosphere.
Desorption: when the adsorbent is saturated, it loses its adsorption function and needs to be regenerated. The adsorbent is mainly gasified by heat source and then carried out by the carrier.
Purge: in the process of heating and gasification of adsorbate, the adsorbent is also heated correspondingly. Low temperature is conducive to adsorption, so it is necessary to reduce the temperature of adsorbent.
Product features and advantages
Advanced design concept: system integration, standardized / modular design makes the construction period more flexible / turnkey project, so that customers can leave the project to expert.
Large adsorption capacity: fast adsorption and regeneration, high adsorption efficiency and high recovery rate
Excellent and efficient operation performance: processing efficiency is above 90%.
Reliable safety performance: multiple monitoring and warning / multiple safety interlock to ensure efficient and safe operation.
Convenient and fast network interaction performance: remote control, real-time online monitoring.
Simple and efficient operation performance: modular management, programmed control, automatic operation / simple, efficient, fast, easy maintenance.
Application industry
It is suitable for pharmaceutical, film coating, painting, high strength and high modulus polyethylene (PE fiber and diaphragm), semiconductor Polymer materials, packaging printing, leather making (superfine fiber), petrochemical industry, etc.
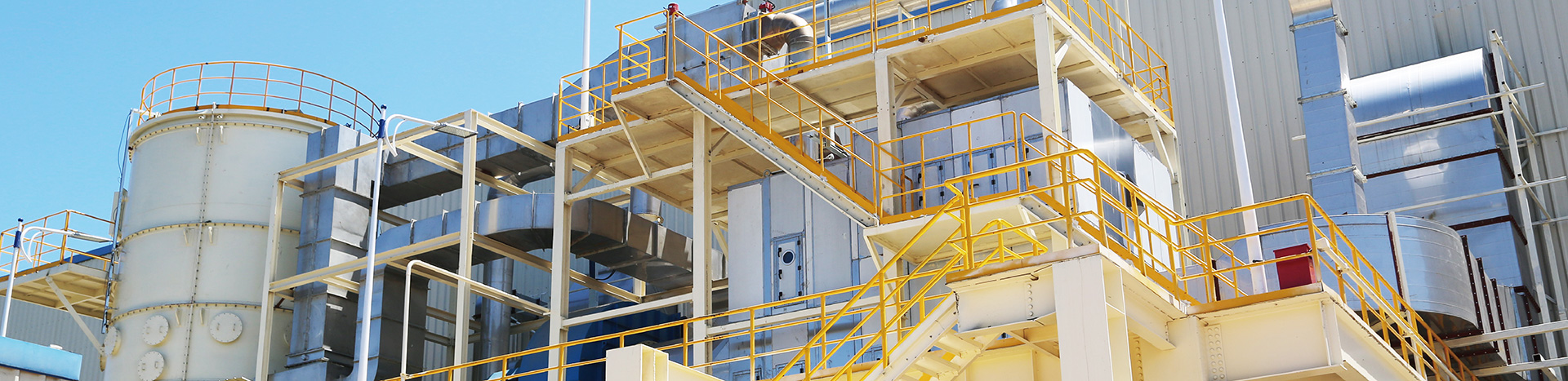
Product overview
(Activated carbon fiber (ACF) adsorption recovery device is a device which uses activated carbon fiber (ACF) as adsorption material, through advanced, efficient, safe and reliable process, mechatronics automatic control technology to treat the organic waste gas from various industries in the production process, and fully recover the organic solvent in the industrial waste gas.
1.The adsorber can be divided into four cores, eight cores, ten cores and twelve cores.
2.Applicable conditions waste gas component: single component, with recycling value.
Process principle description
ACF adsorber (attached)
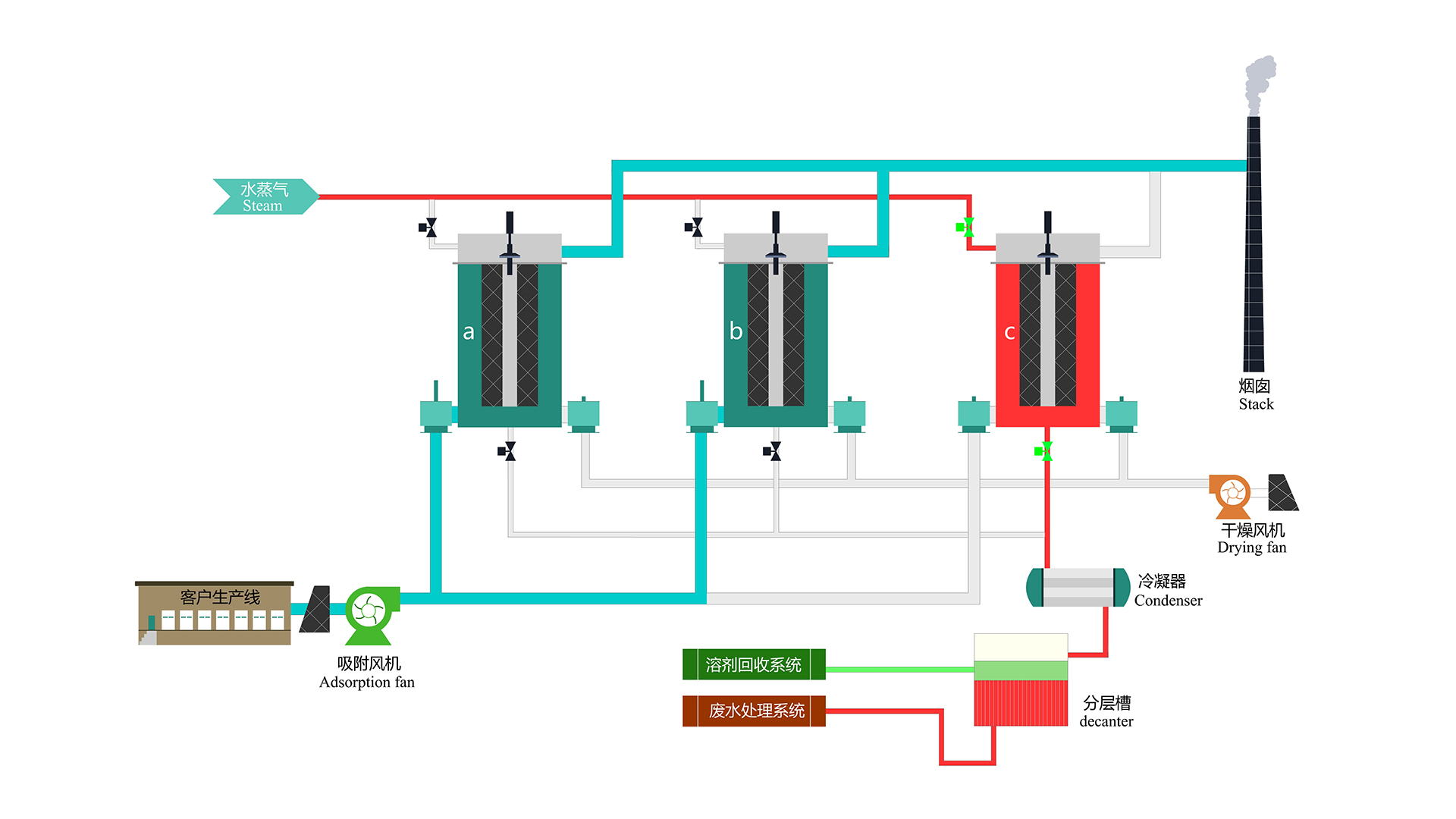
After the organic waste gas enters the adsorber, it circulates through the following three processes.
Adsorption process: the organic solvent in the exhaust gas is adsorbed on the surface of ACF adsorption material.
Desorption process: the organic solvent on the surface of the adsorption material is desorbed by water vapor, and then condensed and recovered.
Drying process: hot air or room temperature air is introduced to dry the adsorption material, remove the water on the surface, and reduce the temperature at the same time.
Product features and advantages
Advanced design concept: system integration, standardized / modular design make the construction period more flexible. /Turnkey project | |
Large adsorption capacity: fast adsorption and regeneration, high adsorption efficiency and high recovery rate | |
Simple and efficient operation performance: modular management, programmed control, automatic operation / simple, efficient, fast, easy maintenance. |
Application industry
It is suitable for organic gas recovery from chemical, pharmaceutical, polymer materials, hydrogen peroxide, insulating materials and other industries.
Component: single component, with recycling value.
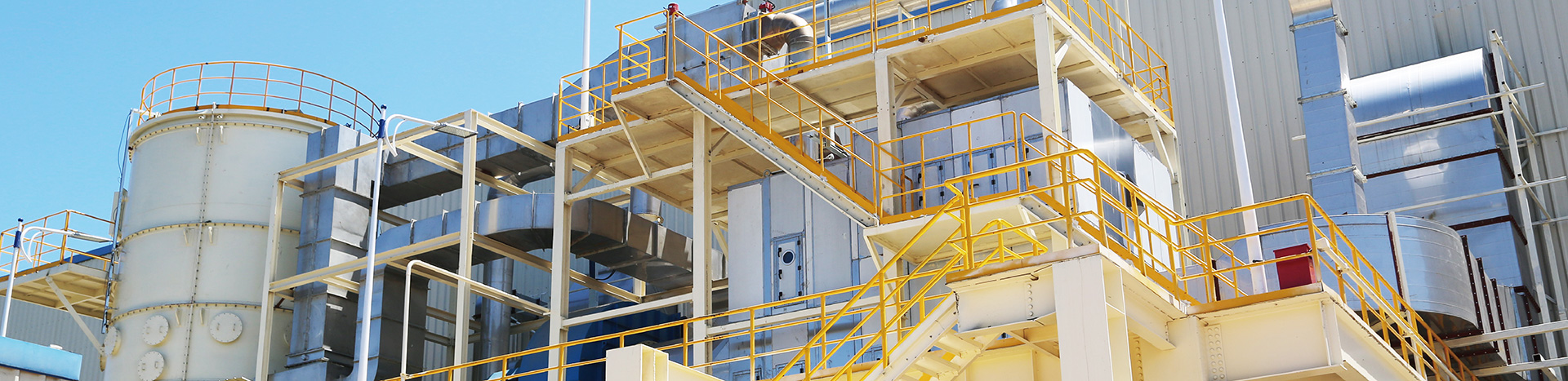
Product overview
Adsorption concentration unit is a new generation of VOCs treatment equipment independently developed by Huashijie. It is a method that organically combines the adsorption concentration unit and the thermal oxidation unit. It is mainly aimed at the organic waste gas with large air volume and low concentration. After adsorption purification and desorption, it is converted into organic waste gas with small air volume and high concentration for thermal oxidation treatment, and the heat released by organic matter combustion is effectively utilized.
Process principle description
Process schematic diagram
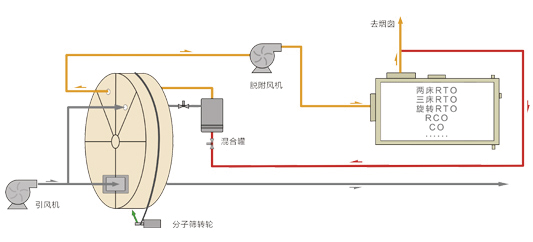
Technological features
Characteristics of molecular sieve rotor + RTO combination process:

Oxidation temperature ~ 800 ℃
The heat transfer efficiency is more than 95% when the regenerative ceramic is used as the heat exchanger
The treatment efficiency is 90% - 99%
The floor area is relatively moderate
Maximum temperature resistance ~ 1000 ℃
Can deal with sulfur, halogen and other organic substances
Suitable for continuous operation
Characteristics of molecular sieve rotor + CO combination process:
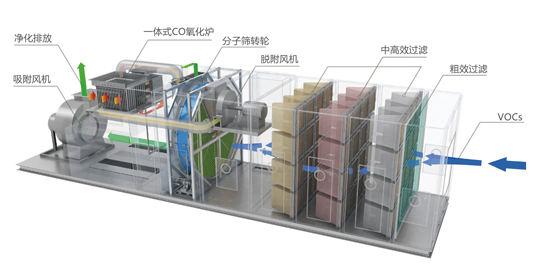
Oxidation temperature ~ 300 ℃
Tube or plate type heat exchanger is used, and the heat exchange efficiency is about 65%
Treatment efficiency 90% - 99%
The floor area is relatively small
Maximum temperature resistance ~ 500 ℃
Cannot deal with sulfur, halogen and other organic substances
Suitable for intermittent operation
Application industry
Exhaust gas treatment of various painting workshops (automobile manufacturing, shipbuilding, bicycle manufacturing, aircraft manufacturing, metal products, etc.)
Exhaust gas treatment of various printing workshops (gravure printing, building decoration material printing, other printing processes)
Exhaust gas treatment of aluminum profile production and coating process
Exhaust gas treatment in the manufacturing process of various electronic products
Exhaust gas treatment in the manufacturing process of semiconductor integrated circuit and liquid crystal display (LCD)
Exhaust gas treatment of lithium ion battery manufacturing (electrode forming process, electrolyte filling process)
Exhaust gas treatment in the production process of resin, rubber, tire and other products
Exhaust gas treatment of volatile organic compounds from automobile repair shop and dry cleaning shop
Treatment of exhaust gas containing nitrogen, sulfur, chlorine and other impurities
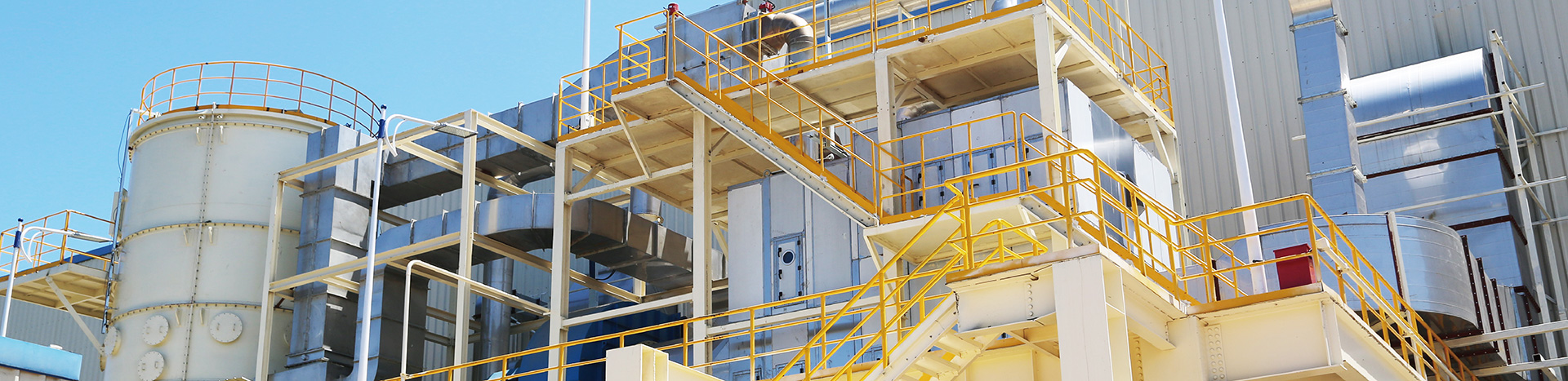
Product overview
Honeycomb activated carbon adsorption treatment of organic waste gas is to make use of the characteristic of activated carbon micropores that can absorb organic substances to absorb the organic waste gas of large volume low concentration in the organic solvent to activated carbon and concentrated it, the clean gas directly discharged after adsorption purification. Catalytic combustion desorption is to heat the adsorbed organic solvent in the activated carbon to the boiling point by using the hot air generated from the decomposition of organic waste gas in catalytic combustion, and then introduce the concentrated high concentration waste gas into the catalytic combustion device for thermal oxidation reaction and discharge after reaching the standard.
Air volume: 5000-100000 nm 3 /h
Components: organic waste gas
Concentration: ≤ 1000mg/nm 3
Process principle description
Honeycomb activated carbon adsorption bed
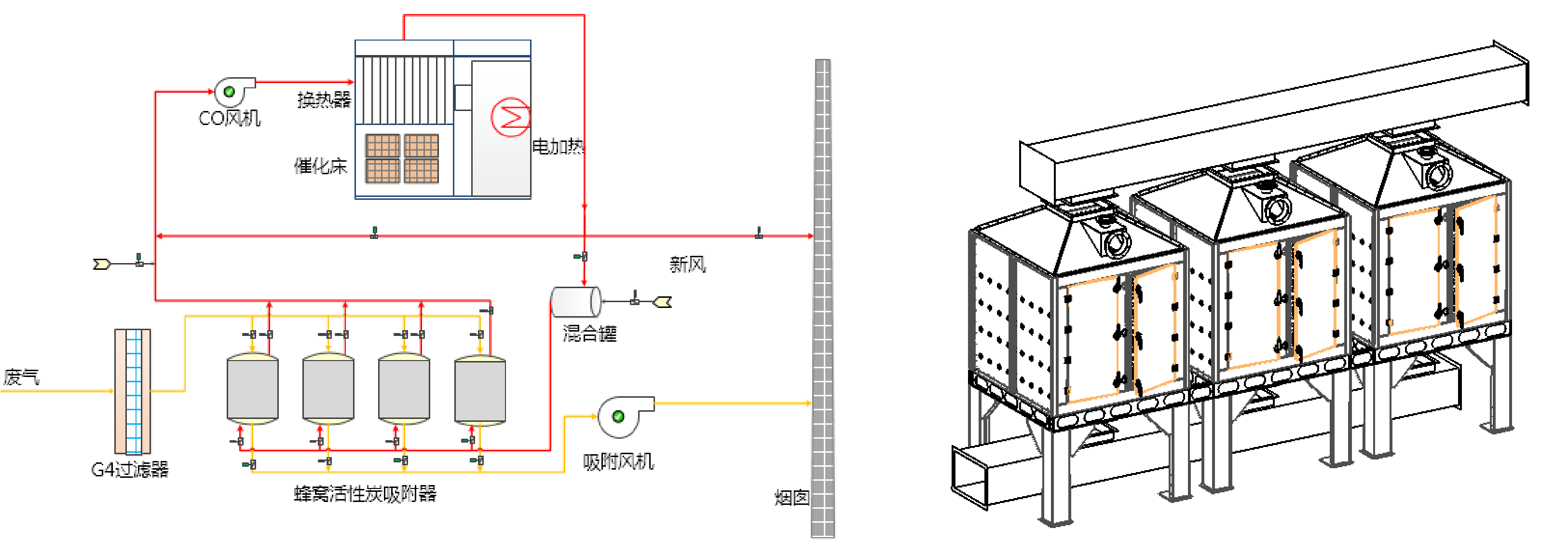
The principle of honeycomb activated carbon adsorption catalytic combustion desorption is to make use of the strong adsorption characteristic of activated carbon and low boiling point of organic solvent, first use activated carbon adsorption, when the activated carbon adsorption reaches saturation, start the catalytic combustion device, use electric heating to produce a small amount of hot air about 60 ~ 120 ℃ to heat the saturated activated carbon, so that the organic solvent in the activated carbon reaches boiling point to desorption After the thermal oxidation reaction, the high concentration waste gas entering the catalytic combustion device becomes clean and harmless gas and is directly discharged, or enters the heat exchange device, and the high concentration waste gas desorbed from the activated carbon is preheated in the heat exchange device to achieve the goal It is close to the temperature of thermal oxidation, and then the thermal oxidation reaction is carried out in the catalytic combustion device. In this way, only a small amount of heat is provided by the electric heater to reach the thermal oxidation temperature, which reduces the power of the electric heater of the catalytic combustion device, makes the catalytic combustion device and the desorption process of activated carbon achieve low power operation, and reduces the operation cost.
Technological features
1.High adsorption efficiency and strong adsorption capacity
Honeycomb activated carbon has larger specific surface area, higher adsorption efficiency and stronger adsorption capacity than granular carbon and columnar carbon.
2.Wide range of application
Honeycomb activated carbon is suitable for sulfur dioxide, nitrogen oxides, nitrogen oxides, aromatic compounds and other major air pollutants, as well as various toxic and harmful gases, volatile VOC gases and organic solvents emitted by industrial and mining enterprises.
3.Small area, simple maintenance and high efficiency
Honeycomb activated carbon equipment has compact structure, small floor area, simple and convenient maintenance and management, low operation cost, and the purification rate of organic waste gas after adsorption treatment by honeycomb activated carbon method is more than 90%.
Product features and advantages
Advanced design concept: system integration, standardized / modular design makes the construction period more flexible / turnkey project, so that customers can leave the project to experts. |
Scientific and rigorous design means: Fluent software is used for numerical simulation / optimization of the internal flow field distribution of activated carbon bed equipment. |
Excellent and efficient operation performance: treatment efficiency above 90%. |
Reliable safety performance: multiple monitoring and early warning / multiple safety interlock to ensure efficient and safe operation. |
Convenient and fast network interaction: remote control, real-time online monitoring. |
Simple and efficient operation performance: modular management, programmed control, automatic operation / simple and efficient, convenient and fast maintenance. |
Appearance of the equipment: the activated carbon bed adopts sheet metal structure design as a whole, neat and beautifully presented with few welding parts. |
Application industry
Suitable for coating, spraying, printing, chemical industry and other industries.
Air volume: 5000 ~ 100000 Nm3 / h
Component: organic waste gas
Concentration: ≤ 1000mg / Nm3
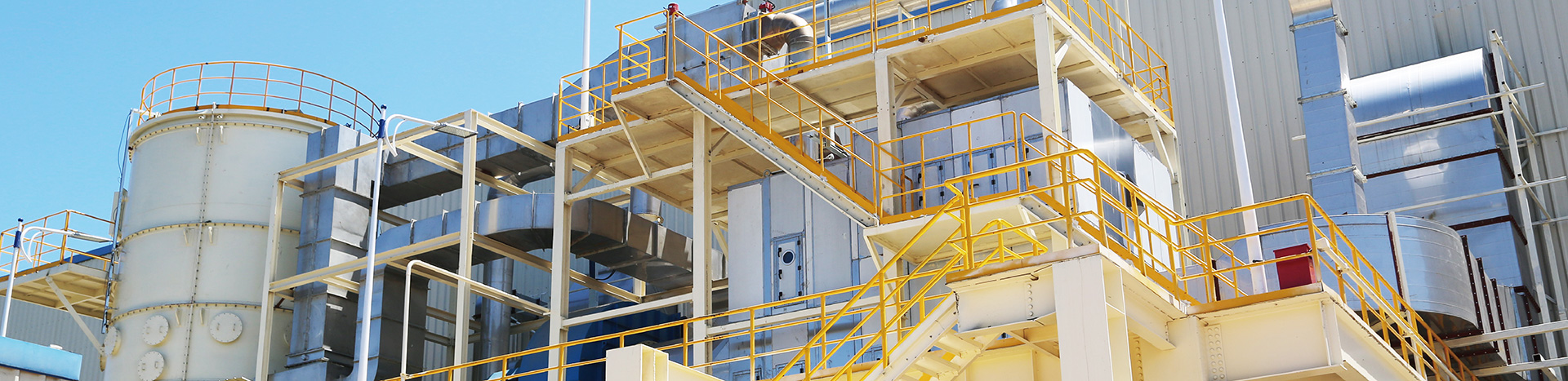
Product overview
The basic principle of regenerative thermal oxidizer is to oxidize organic waste gas (VOCs) to CO2 + H2O at high temperature (≥ 760 ℃). The purification efficiency is as high as 99%. The high temperature gas produced by oxidation flows through the special ceramic regenerator to make the ceramic body warm up and "store heat". The next process is that the waste gas passes through the ceramic which has "stored heat" and transfers the heat of the ceramic to the waste gas. The organic waste gas passes through the ceramic as the carrier of the heat exchanger for repeated heat exchange, so as to save the fuel consumption of waste gas heating and reduce the operation cost. The heat recovery efficiency is as high as 95%。Under the condition of medium and high concentration, RTO can output waste heat and make use of it in the form of steam, hot air and hot water, so as to achieve economic benefits while meeting the environmental protection objectives.
Process principle description
Rotary RTO
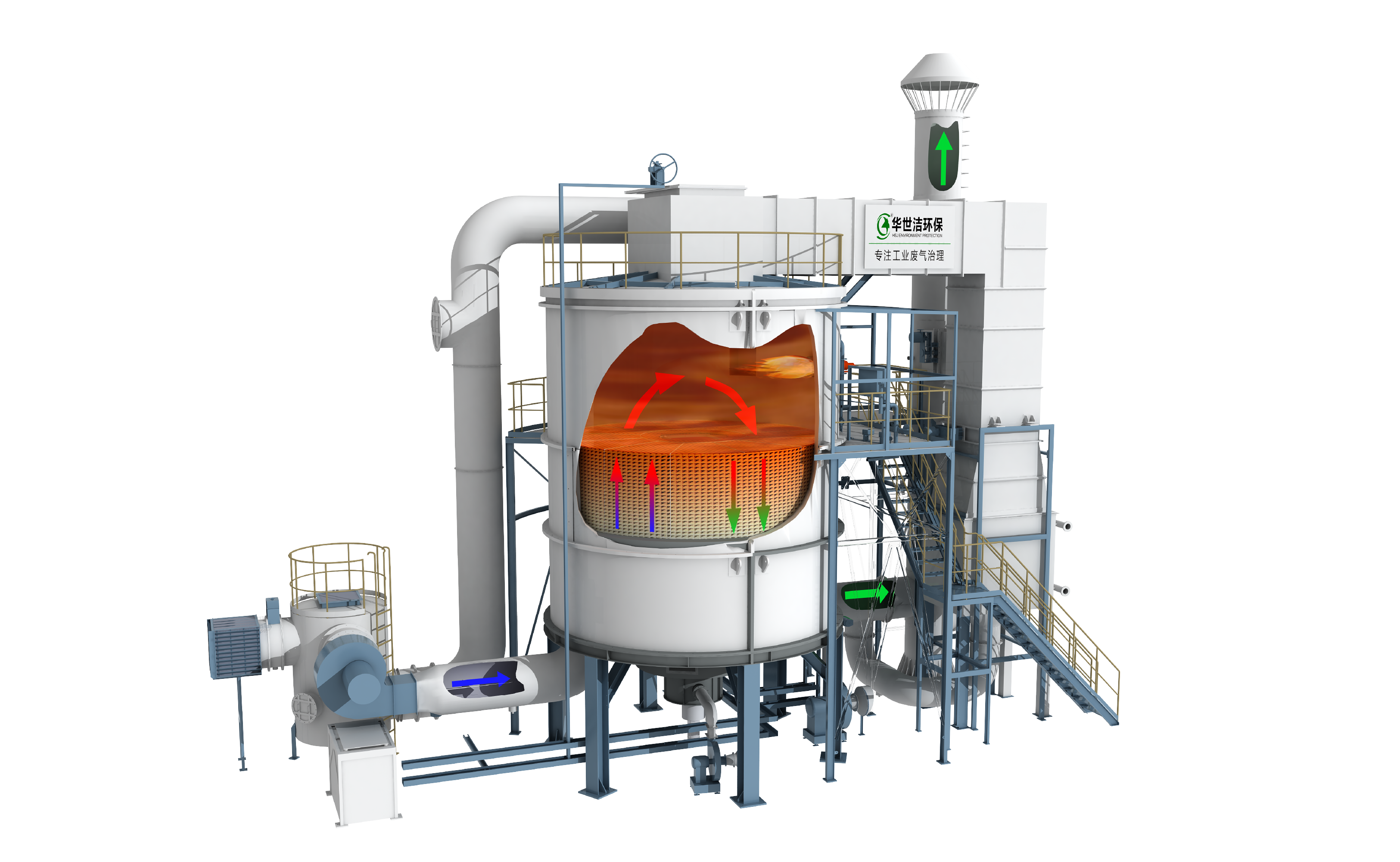
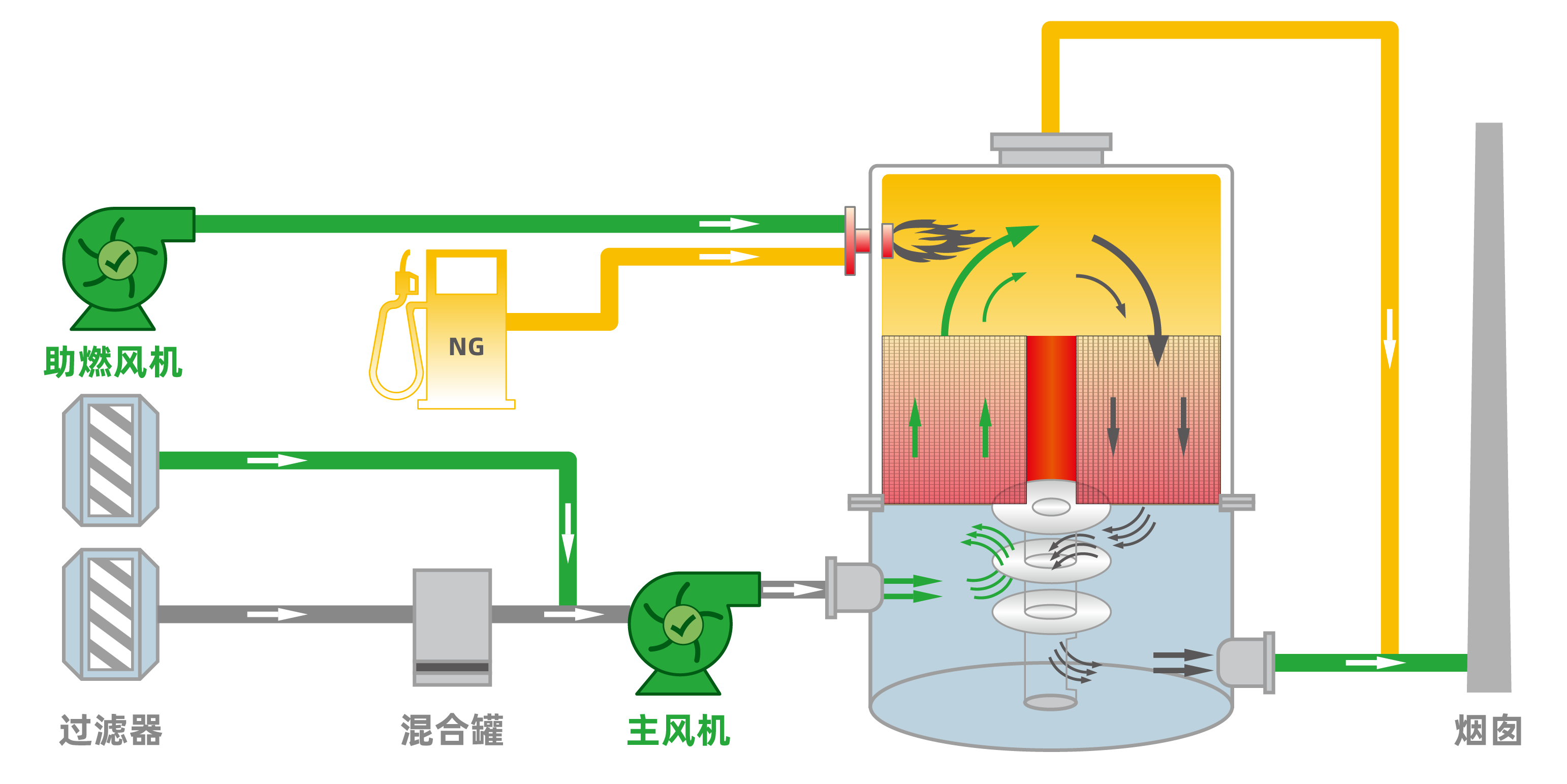
Rotary RTO is to change the position of the exhaust gas into the ceramic through the rotation of the rotary wing, so as to realize the alternate conversion of the heat storage zone and the heat release zone. The ceramic regenerator is divided into 12 zones, five air inlet zones, five air outlet zones, one purging zone and one dead zone. Each heat storage zone experiences the process of heat storage, heat release and purging in turn, and works continuously.
Three bed RTO
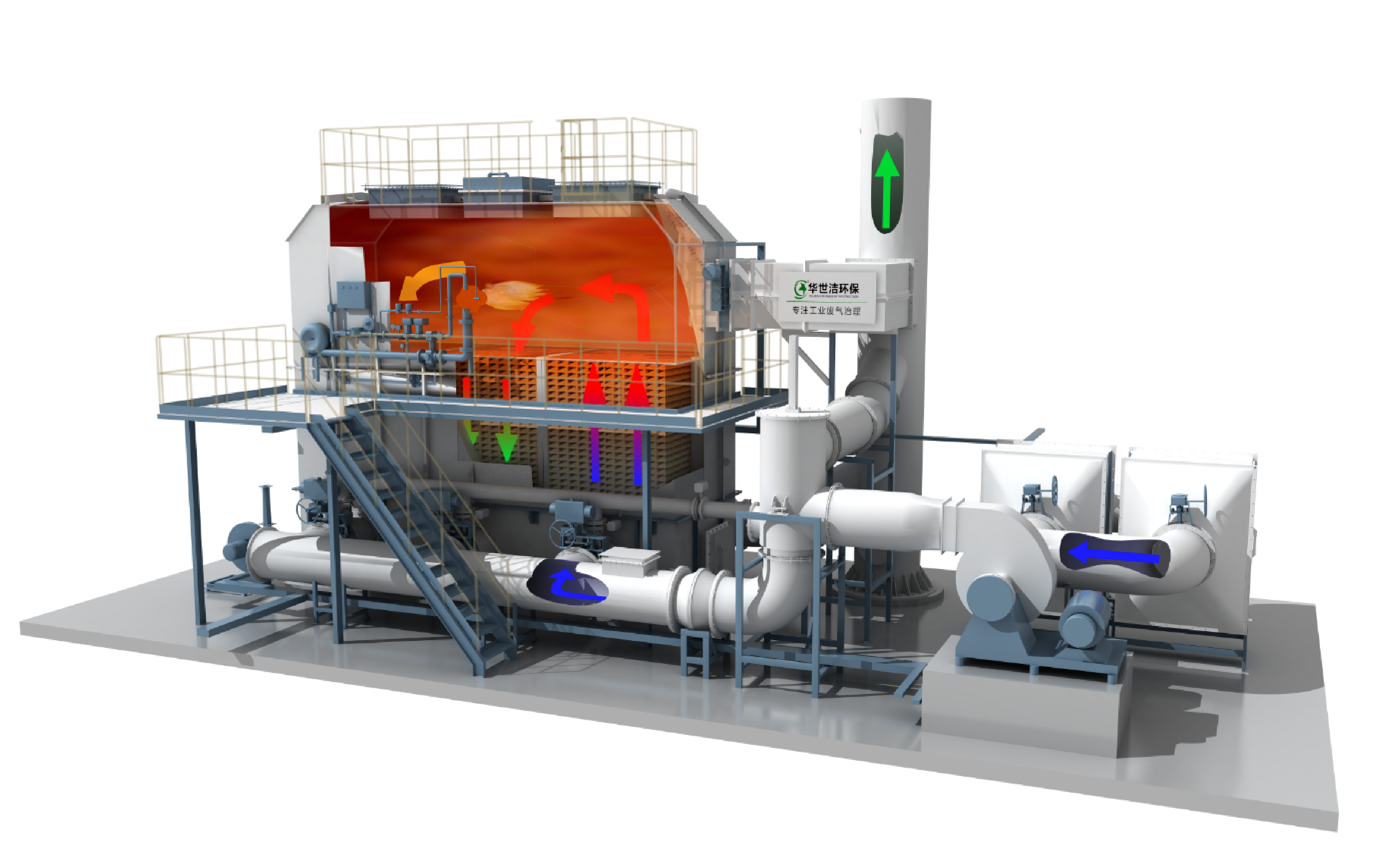
The organic waste gas to be treated enters the ceramic medium layer of regenerator 1 (the ceramic medium "stores" the heat of the previous cycle). The ceramic releases heat and the temperature decreases, while the organic waste gas absorbs heat and the temperature increases. After leaving the regenerator, the waste gas enters the oxidation chamber at a higher temperature. At this time, the temperature of the waste gas depends on the volume of the ceramic body, the flow rate of the waste gas and the geometric structure of the ceramic body . In the oxidation chamber, the organic waste gas is heated by the burner to the set oxidation temperature of 760 ℃, so that the VOC component is decomposed into carbon dioxide and water. Since the exhaust gas has been preheated in the regenerator, the fuel consumption is greatly reduced. The oxidation chamber has two functions: one is to ensure that the exhaust gas can reach the set oxidation temperature, the other is to ensure that there is enough residence time to fully oxidize VOC in the exhaust gas. The waste gas is incinerated in the oxidation chamber to become purified high-temperature gas, and then leaves the oxidation chamber and enters the regenerator 2 (which has been cooled in the previous cycle). After heat release and cooling, the waste gas is discharged, while the regenerator 2 absorbs a lot of heat and then heats up (for heating the waste gas in the next cycle). The purified waste gas is discharged into the atmosphere through the chimney, and a small stream of purified gas is introduced to clean the regenerator 3. The exhaust temperature is about 40 ℃ higher than the intake temperature. After the cycle is completed, the inlet and outlet valves are switched once, and then enter the next cycle. The exhaust gas enters from the heat storage chamber 2 and the heat storage chamber 3 is discharged. At the same time, a part of purified gas is introduced to clean the heat storage chamber 1. Work continuously and again.
Product features and advantages
Advanced design concept: system integration, standardized / modular design makes the construction period more flexible / turnkey project, so that customers can leave the project to experts. |
Scientific and rigorous design means: Fluent software is used for numerical simulation to optimize the internal flow field and temperature field distribution / system of RTO equipment |
Bentley layout; the system is more reasonable and the operation and maintenance cost is more economical. |
Excellent and efficient operation performance: top level configuration of components, focusing on operation stability/ The heat transfer efficiency is more than 95%, and the treatment efficiency is as high as 99%. |
Reliable safety performance: Super explosion-proof design, top safety accessories / LEL advanced monitoring and early warning, multiple safety interlock / ensure efficient and safe operation. |
Convenient and fast network interaction performance: remote control, real-time online monitoring. |
Simple and efficient operation performance: modular management, programmed control, automatic operation / simple and efficient, convenient and fast maintenance. |
Application industry
Suitable for painting, spraying, chemical, pharmaceutical, printing and other industries.
Air volume: 1000 ~ 1000000nm 3/h
Component: the component is complex, has no recycling value, and is difficult to reuse
Concentration:1000mg/Nm3<concentration<25%LEL
The inlet temperature of rotary RTO is not higher than 100℃, and that of bed RTO is not higher than 200℃
Rotary RTO requires no corrosion components in exhaust gas
持续开发中。敬请期待!
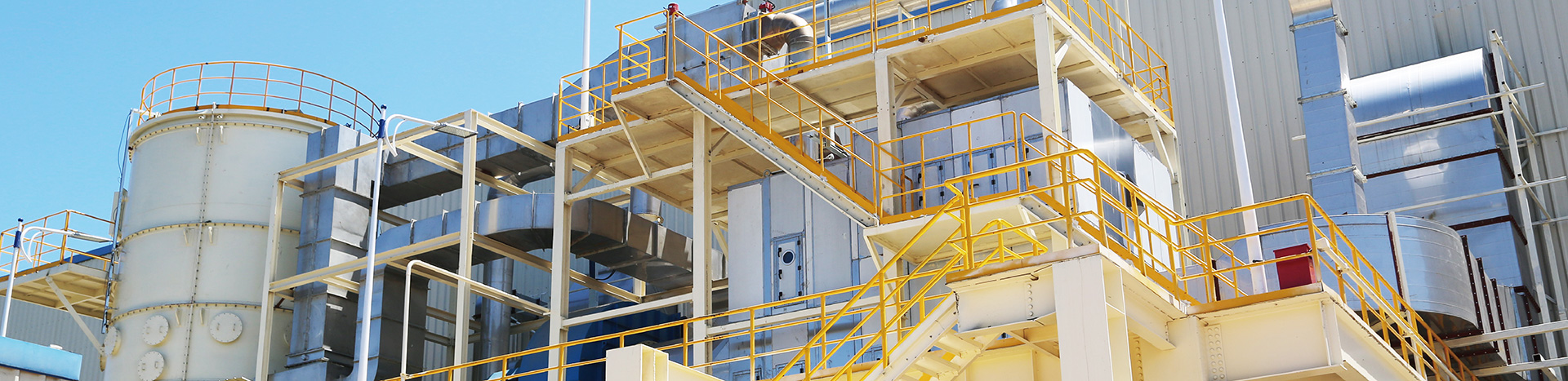
Product overview
Co uses catalytic combustion technology to make the organic waste gas burn without flame under the condition of lower starting temperature (300-400 ℃). In the process of catalytic combustion, the catalyst can reduce the activation energy, and the surface of the catalyst has adsorption function, which makes the reactant molecules concentrate on the surface to improve the reaction rate and accelerate the oxidation process. Compared with direct combustion, the catalytic combustion of organic waste gas has the characteristics of low starting temperature and low energy consumption. In some cases, no external heating is required after the ignition temperature is reached. The purification rate of organic waste gas treated by catalytic combustion is generally over 95%, and the final product is harmless CO2 and H2O (heteroatom organic compounds and other combustion products), so there is no secondary pollution. Co uses high performance catalyst, Pt and PD noble metal catalyst with ceramic support. The dispersion of noble metal active position is high, catalytic activity is high, service life is long, pressure loss is small, which reduces the total energy consumption of the whole machine.
Process principle description
CO
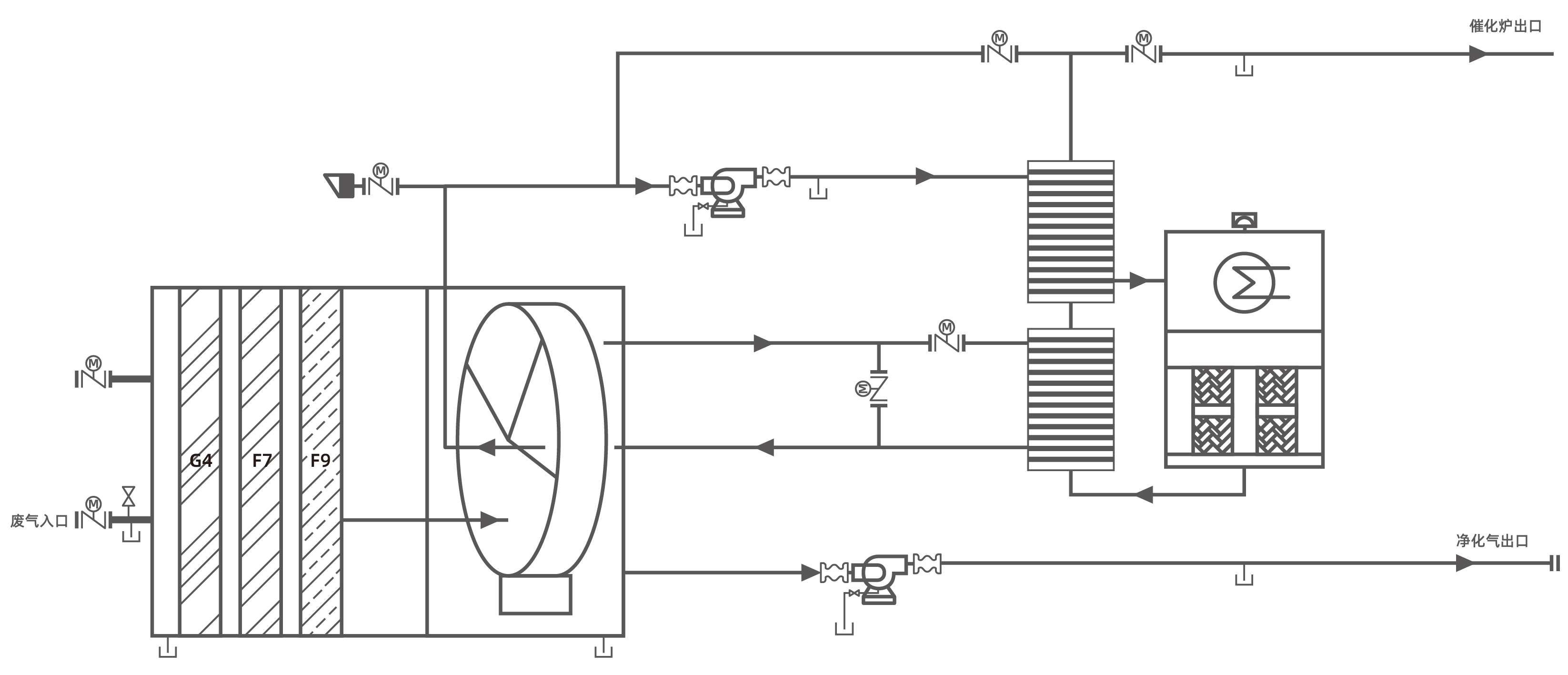
VOCs flow direction 1: driven by the desorption fan, low concentration VOCs gas from the cooling area of the molecular sieve rotor enters the cold side channel of the first stage heat exchanger for heat exchange, and the gas temperature rises from 60 ℃ to 200 ℃ and then flows back to the desorption sector of the molecular sieve rotor. High temperature gas desorbs a large number of VOCs molecules from the zeolite surface of the molecular sieve rotor to form high concentration VOCs, and the concentration is controlled below 10g / m3.
VOCs flow to two directions Driven by the desorption fan, the high concentration VOCs gas enters the cold side channel of the two-stage heat exchanger for heat exchange. The gas temperature rises from 120 ℃ to 300 ℃ and then enters the catalytic combustion chamber. The temperature meter in the catalytic combustion chamber checks the temperature of the VOCs gas after entering. If the temperature of the VOCs gas is lower than 300 ℃, the burner in the catalytic combustion chamber will ignite automatically to heat the gas again until the temperature is between 300 ℃ and 350 ℃. Then VOCs gas flows through the burner and then flows through the surface of catalyst to produce flameless combustion. The organic molecules in VOCs are oxidized and decomposed into CO2 and H2O, and a lot of heat energy is released at the same time. The specific heat ratio of VOCs is about 25 ℃ / g. when the concentration of VOCs is 10g / M 3, the temperature rises 250 ℃. Therefore, the temperature of 300 ℃ VOCs increases to 550 ℃ after catalytic combustion. After catalytic combustion, VOCs gas is oxidized and decomposed into clean high temperature gas, which flows through the hot side channel of the first stage heat exchanger and the hot side channel of the second stage heat exchanger to provide them with heat energy for heat exchange in the cold side channel, and then discharged into the atmosphere through the chimney. In the later design of waste heat recovery and utilization, the high-temperature and clean gas will also be recycled to provide heat energy for Party A's production workshop, hot water supply or environmental heating supply.
Product features and advantages
Advanced design concept: system integration, standardized / modular design makes the construction period more flexible / turnkey project, so that customers can leave the project to experts. |
Scientific and rigorous design means: using FLUENT software for numerical simulation/ The distribution of flow field and temperature field in CO equipment was optimized. |
Excellent and efficient operation performance: treatment efficiency up to 95% |
Reliable safety performance: explosion proof design, insulation monitoring and early warning / multiple safety interlock, to ensure efficient and safe operation. |
Convenient and fast network interaction performance: remote control, real-time online monitoring. |
Simple and efficient operation performance: modular management, programmed control, automatic operation / simple and efficient, convenient and fast maintenance. |
Application industry
Suitable for painting, spraying, printing and other industries
Air volume: 5000 ~ 1000000nm 3 / h
Components: ethyl acetate, propyl acetate, ethanol
Concentration: 200mg / Nm3 < concentration < 1200mg / Nm3
The inlet temperature of RCO is not lower than 300 ℃, and the outlet temperature is not higher than 600 ℃



分子筛转轮
高效净化一体机

环保持续达标 • 保障面面俱到
分子筛转轮优势·核心材料自主研发:

Napotec®分子筛吸附浓缩转轮分为吸附区、脱附区、冷却区,转轮在各个区域连续运转

高效净化一体机优势


行业全面选型多
服务完善网点多
3大系列200+产品组合
全国70+家服务网点

供货安装速度快
一键启动开机快
供货周期30天
开机时间30分钟

治理达标效果好
安全稳定性能好
净化效率90~99%
转轮寿命5~10年

投资经济成本低
运维合理能耗低
投资成本降低50%
运维费用降低30%
整体吊装 一步到位

移动式 运输便捷 搬移方便


整体吊装
设备卸车=完成安装
1天安装完成,通电即用

安装便捷

操控简单
一体机产品系列
SL-C型
推荐优选
风量 5000~50000Nm³/h
浓度 0~1200mg/m³
“一字型”整体运输整体吊运
安装即用,一步到位。

UD-C型
推荐优选
风量 60000~120000Nm³/h
浓度 0~1200mg/m³
复式双层结构
安装简便,占地面积小

MO-C型
推荐优选
风量 120000~200000Nm³/h
浓度 0~400mg/m³
模块化组装
全风量下可定制化设计
适应性更高

智能化批量化生产

15000㎡生产车间
生产能力1天/台
非标设备模块化·模块设备批量化
应用行业

涂装

涂料油墨

涂布复合

烟包

软包装

化工

医药

新材料

半导体

橡胶
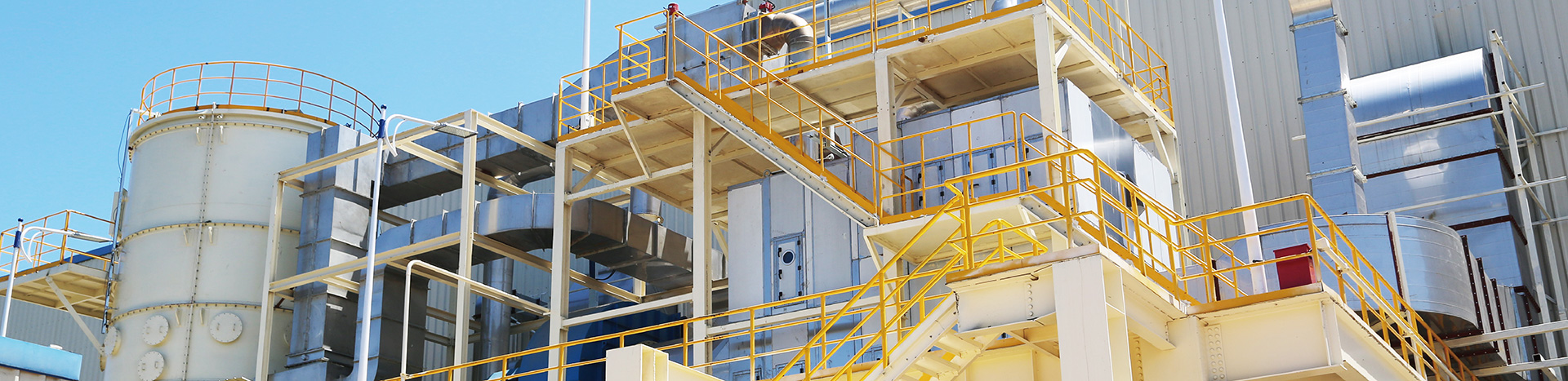
Overall introduction of the equipment
The device is an integrated box type device integrating biological trickling filter and biological filter module, spray humidification system, fan, air duct, heating device, power distribution cabinet, frequency converter, electrical appliance, instrument and PLC automatic control system. Modular and standardized design, mass production, effective cost reduction, faster delivery.
Core advantage
Independent core materials: huashijie's strong R & D team / ensures the core competitive advantage of products / all core materials have independent intellectual property rights and independent production |
Modularization of non-standard equipment: standardized production, guaranteed product quality, standard parts, faster installation and replacement, modular production, more beautiful product design |
Mass production of modular equipment: mass production, reduction of production cost / assembly line operation, improvement of production efficiency / automatic production line, guarantee of product quality |
High quality project: fine construction / quality service / Systematic Guarantee |
technological process
Huashijie biological treatment process is composed of biological trickling filtration and biological filtration. It is also called two-stage biological process. It can treat both soluble and insoluble pollutants. The rear fan is adopted, and the negative pressure inside the device works to reduce the emission of waste gas to the environment as much as possible.
The process flow of two-stage biological waste gas treatment is as follows:
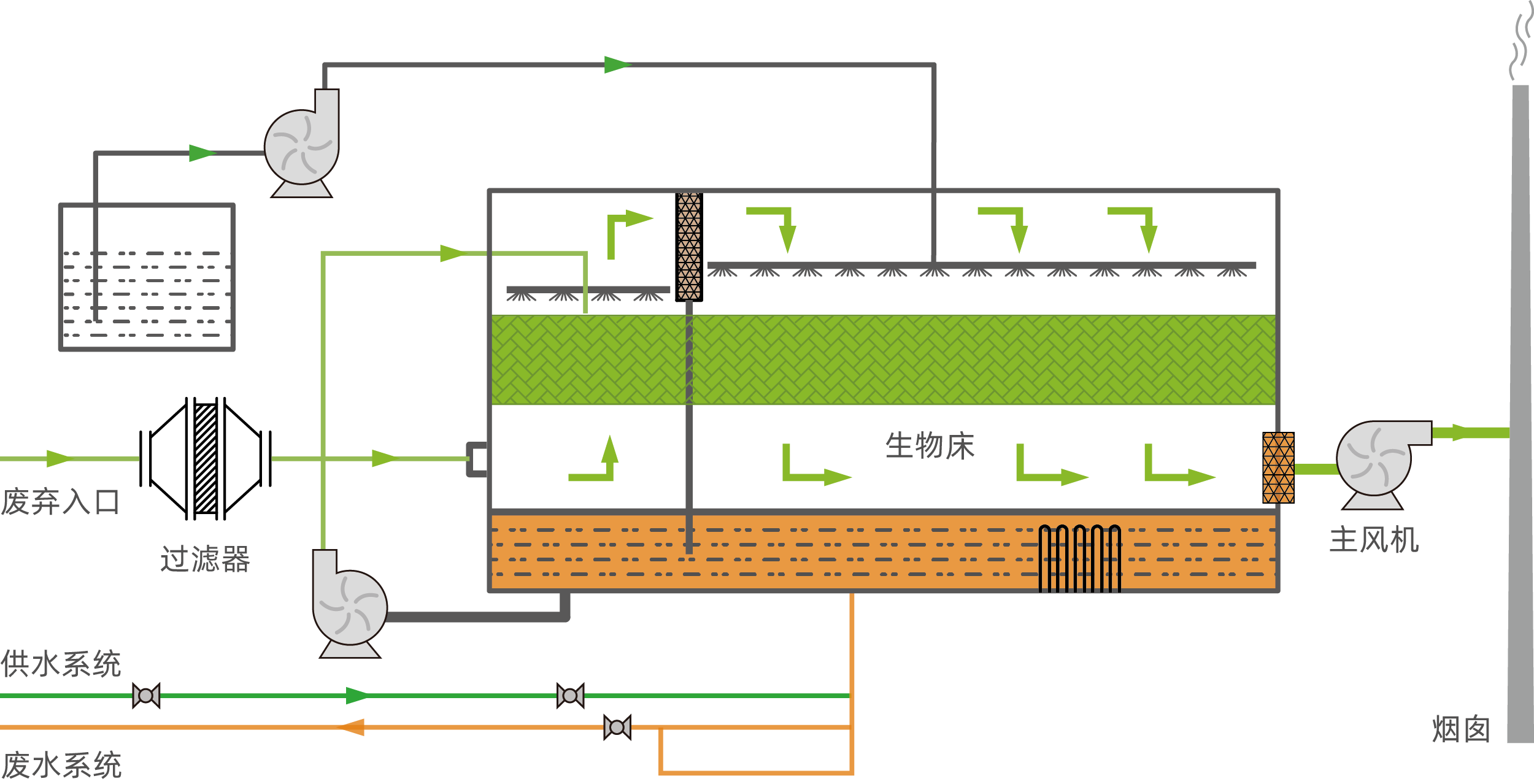
After the waste gas enters the device, the biotrickling section in the device and the spray liquid exchange gas and liquid reversely on the packing surface. Most of the soluble pollutants are transferred from the gas phase to the water phase, and the spray liquid circulates. The pollutants in the water phase are used by the microorganisms attached to the packing surface, and are degraded into harmless substances through microbial life activities.
The insoluble pollutants enter the biofilter section with the waste gas, and are captured by the biofilm attached to the surface of the filler, and are digested as nutrients to further realize the harmless treatment of pollutants. The waste liquid produced by the microbial system can be discharged into the sewage system of the plant or the sewage treatment plant due to the absence of harmful substances and B / C ≥ 0.3.
working principle
The pollution substances in the waste gas components are transformed into carbon dioxide, water, polysaccharides, protein organic substances and microbial cell components, inorganic salts and other low harmful or harmless substances by using the life metabolism activities of microorganisms, so as to realize the effective treatment of the components of waste gas pollutants. The process of the transformation of pollutants in micro objects is shown in the following figure:

涂装/涂料行业一体机选型表

工程设备定制电话:15965555490
*上表适用于涂装/涂料行业,其他行业持续更新中,如上述配置无法满足您的要求,请拨打工程定制电话,我们将为您提供更高效的工业废气治理解决方案。
- • VOCs adsorption and concentration treatment
- • Thermal oxidation/catalytic oxidation
- • Adsorption and recovery of high concentration VOCs
- • Biological treatment of odor VOCs
- • Industrial dust and oil mist filtration
- • Heat recovery
- • Dehumidification
- • Indoor purification
- • VOCs Online Monitoring Platform