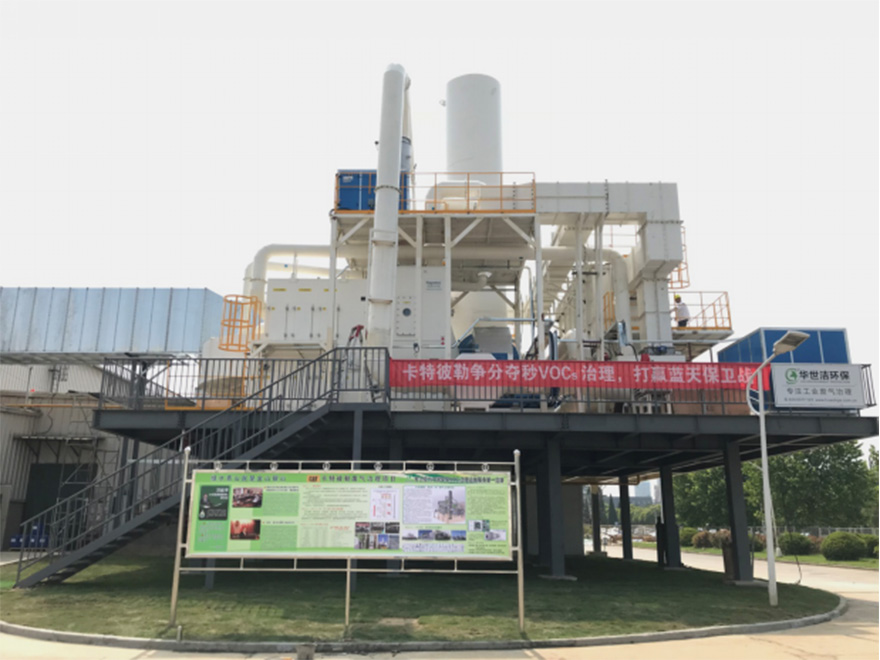
Technology Overview
The catalytic oxidation technology is to heat the waste gas to ~ 300 ℃ for catalytic combustion, so that VOCs in the waste gas can be oxidized and decomposed into CO₂and H2O. In the process of catalytic combustion, the role of the catalyst is to reduce the activation energy of the reaction and make the reactant molecules enrich on the surface of the catalyst to improve the reaction rate. The catalyst is loaded with noble metals of Pt and Pd, with low ignition temperature, ~ 99% purification efficiency, fast start-up and less one-time investment. The catalyst is a chemical reaction on surface, if solid matters accumulated on the ceramic surface for a long time, the catalytic efficiency will be reduced.
Technology application
Catalytic oxidation technology is used in the occasion of small air volume and high concentration. It can deal with benzene, alcohol, ester, alkane, ether and other waste gases, but it cannot deal with gases contain s, halogen, P and other substances that are easy to cause catalyst poisoning and deactivation. It can also be combined with adsorption concentration equipment to treat large air volume and low concentration waste gases, such as painting ink industry, coating industry, packaging and printing industry, semiconductor and other industries.
Molecular sieve rotor + thermal oxidation • Regenerative thermal oxidation RTO • Adsorption recovery
Huashijie's technological advantages
Huashijie independently develops the integrated skid mounted equipment for catalytic oxidation, and has integrated design. The equipment covers a small area, fast start-up. Mass production, short lead time, good quality and cost effiective.
Huashijie independently developed and produced the core material catalyst with selected noble metal catalyst (PT, PD and Au). It has low ignition temperature (280℃), high removal efficiency (> 99%), high catalytic activity, high temperature resistance, oxidation resistance and corrosion resistance. The catalyst changes the chemical reaction speed and does not participate in the reaction itself. There is no consumption before and after the reaction and the service life is long.
- • VOCs adsorption and concentration treatment
- • Thermal oxidation/catalytic oxidation
- • Adsorption and recovery of high concentration VOCs
- • Biological treatment of odor VOCs
- • Industrial dust and oil mist filtration
- • Heat recovery
- • Dehumidification
- • Indoor purification
- • VOCs Online Monitoring Platform