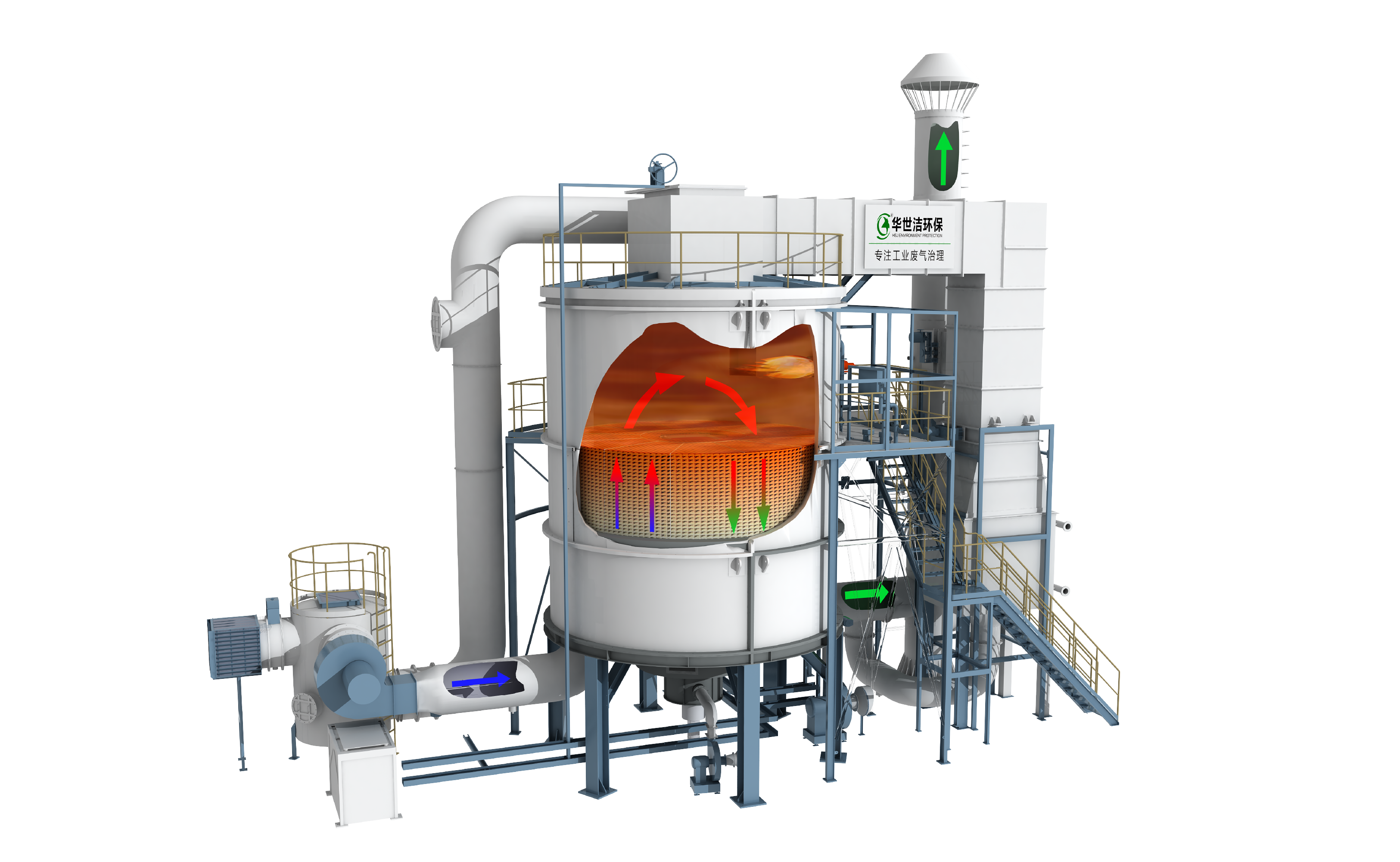
Product overview
The basic principle of regenerative thermal oxidizer is to oxidize organic waste gas (VOCs) to CO2 + H2O at high temperature (≥ 760 ℃). The purification efficiency is as high as 99%. The high temperature gas produced by oxidation flows through the special ceramic regenerator to make the ceramic body warm up and "store heat". The next process is that the waste gas passes through the ceramic which has "stored heat" and transfers the heat of the ceramic to the waste gas. The organic waste gas passes through the ceramic as the carrier of the heat exchanger for repeated heat exchange, so as to save the fuel consumption of waste gas heating and reduce the operation cost. The heat recovery efficiency is as high as 95%。Under the condition of medium and high concentration, RTO can output waste heat and make use of it in the form of steam, hot air and hot water, so as to achieve economic benefits while meeting the environmental protection objectives.
Process principle description
Rotary RTO
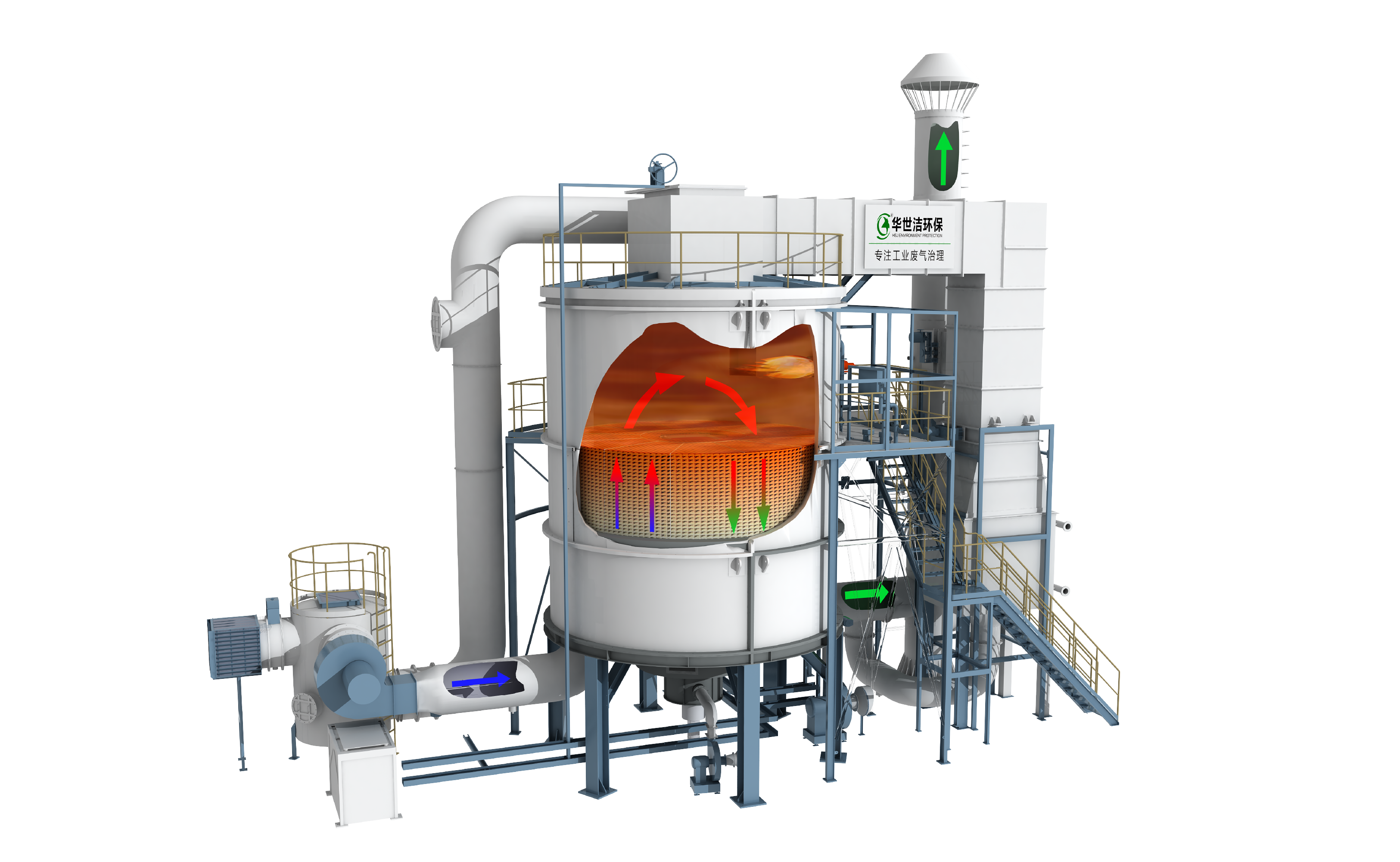
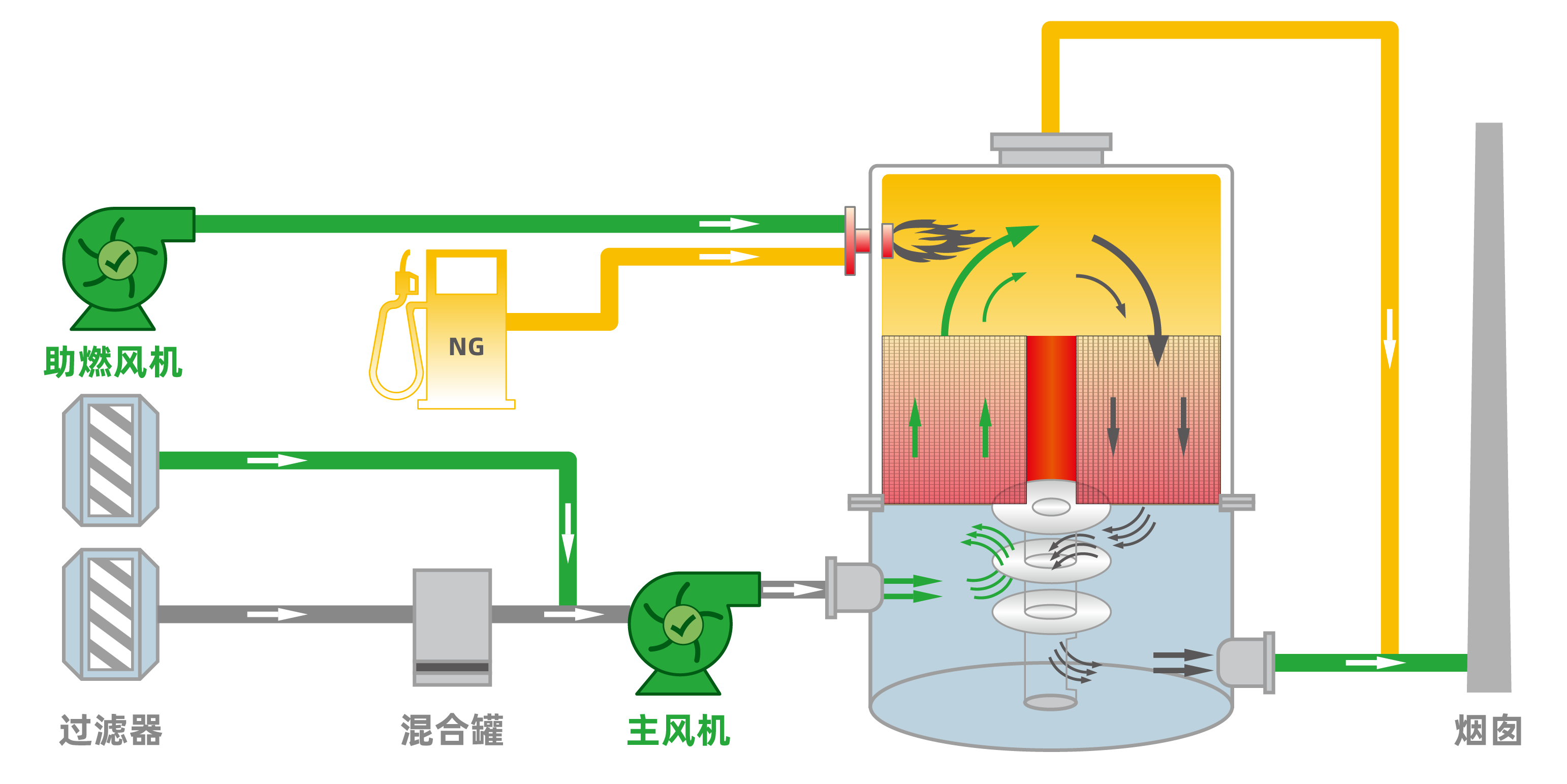
Rotary RTO is to change the position of the exhaust gas into the ceramic through the rotation of the rotary wing, so as to realize the alternate conversion of the heat storage zone and the heat release zone. The ceramic regenerator is divided into 12 zones, five air inlet zones, five air outlet zones, one purging zone and one dead zone. Each heat storage zone experiences the process of heat storage, heat release and purging in turn, and works continuously.
Three bed RTO
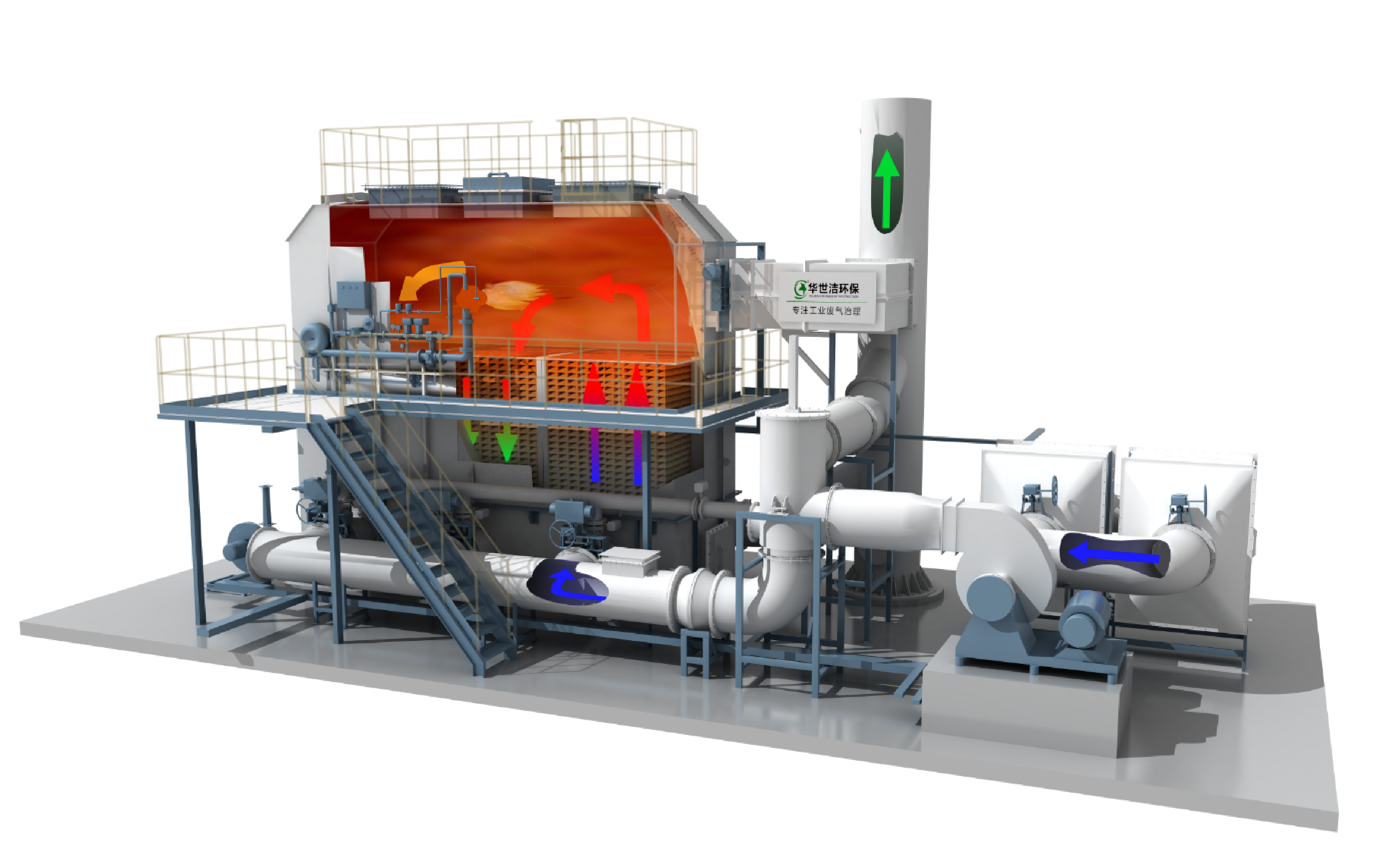
The organic waste gas to be treated enters the ceramic medium layer of regenerator 1 (the ceramic medium "stores" the heat of the previous cycle). The ceramic releases heat and the temperature decreases, while the organic waste gas absorbs heat and the temperature increases. After leaving the regenerator, the waste gas enters the oxidation chamber at a higher temperature. At this time, the temperature of the waste gas depends on the volume of the ceramic body, the flow rate of the waste gas and the geometric structure of the ceramic body . In the oxidation chamber, the organic waste gas is heated by the burner to the set oxidation temperature of 760 ℃, so that the VOC component is decomposed into carbon dioxide and water. Since the exhaust gas has been preheated in the regenerator, the fuel consumption is greatly reduced. The oxidation chamber has two functions: one is to ensure that the exhaust gas can reach the set oxidation temperature, the other is to ensure that there is enough residence time to fully oxidize VOC in the exhaust gas. The waste gas is incinerated in the oxidation chamber to become purified high-temperature gas, and then leaves the oxidation chamber and enters the regenerator 2 (which has been cooled in the previous cycle). After heat release and cooling, the waste gas is discharged, while the regenerator 2 absorbs a lot of heat and then heats up (for heating the waste gas in the next cycle). The purified waste gas is discharged into the atmosphere through the chimney, and a small stream of purified gas is introduced to clean the regenerator 3. The exhaust temperature is about 40 ℃ higher than the intake temperature. After the cycle is completed, the inlet and outlet valves are switched once, and then enter the next cycle. The exhaust gas enters from the heat storage chamber 2 and the heat storage chamber 3 is discharged. At the same time, a part of purified gas is introduced to clean the heat storage chamber 1. Work continuously and again.
Product features and advantages
Advanced design concept: system integration, standardized / modular design makes the construction period more flexible / turnkey project, so that customers can leave the project to experts. |
Scientific and rigorous design means: Fluent software is used for numerical simulation to optimize the internal flow field and temperature field distribution / system of RTO equipment |
Bentley layout; the system is more reasonable and the operation and maintenance cost is more economical. |
Excellent and efficient operation performance: top level configuration of components, focusing on operation stability/ The heat transfer efficiency is more than 95%, and the treatment efficiency is as high as 99%. |
Reliable safety performance: Super explosion-proof design, top safety accessories / LEL advanced monitoring and early warning, multiple safety interlock / ensure efficient and safe operation. |
Convenient and fast network interaction performance: remote control, real-time online monitoring. |
Simple and efficient operation performance: modular management, programmed control, automatic operation / simple and efficient, convenient and fast maintenance. |
Application industry
Suitable for painting, spraying, chemical, pharmaceutical, printing and other industries.
Air volume: 1000 ~ 1000000nm 3/h
Component: the component is complex, has no recycling value, and is difficult to reuse
Concentration:1000mg/Nm3<concentration<25%LEL
The inlet temperature of rotary RTO is not higher than 100℃, and that of bed RTO is not higher than 200℃
Rotary RTO requires no corrosion components in exhaust gas
- • VOCs adsorption and concentration treatment
- • Thermal oxidation/catalytic oxidation
- • Adsorption and recovery of high concentration VOCs
- • Biological treatment of odor VOCs
- • Industrial dust and oil mist filtration
- • Heat recovery
- • Dehumidification
- • Indoor purification
- • VOCs Online Monitoring Platform